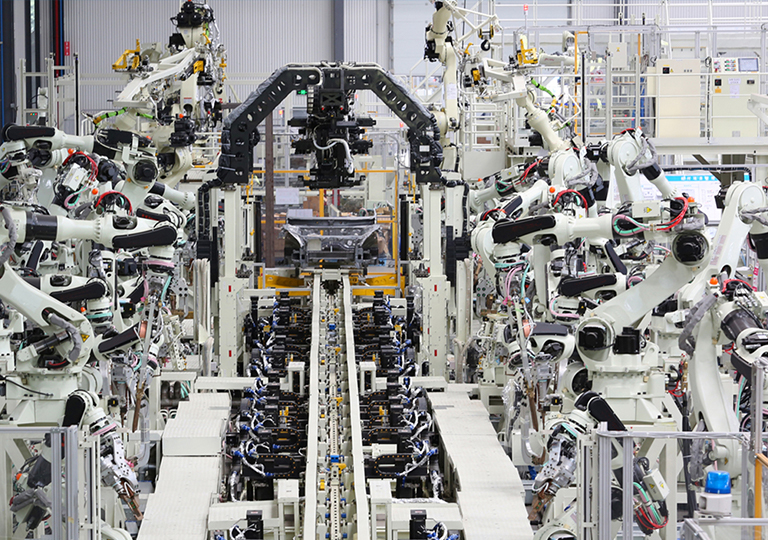
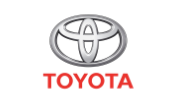
New energy factory white body flexible welding production line
219 robots were used, and multiple innovative advanced technologies such as self-developed ultra high speed conveying, NC flexible positioning system, high-speed rolling, machine vision, etc. were utilized to achieve over 95% equipment utilization rate. The concept of Toyota's lean production and full platform flexible production was fully realized, helping GAC Toyota become a global model factory for Toyota.
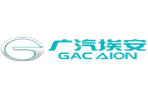
Flexible intelligent welding line for steel aluminum body of new energy vehicles
To provide technical support for the adoption of aluminum body and lightweight design for independent brand new energy vehicles for the first time. In this project, special international advanced connection technology such as nail riveting SPR and FDS hot melt straight drilling, which are not traditional processes, were applied. Through independent application experiments and tests in the early stage, the technology blockade of international giants in this field was successfully broken, providing support for the development of independent brand new energy vehicles.
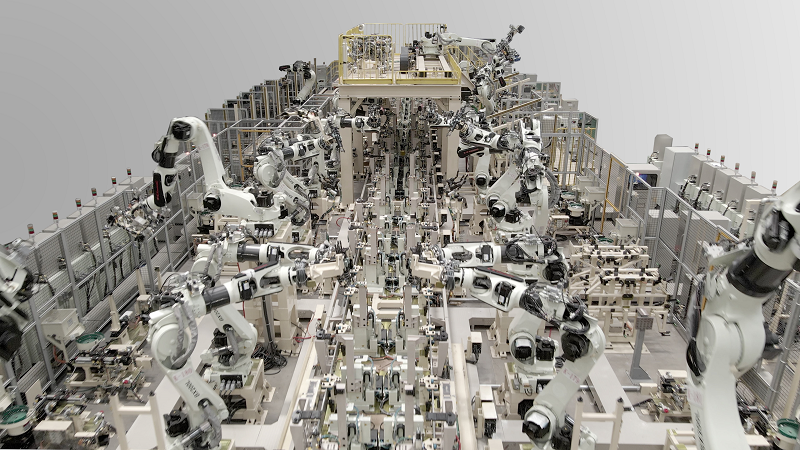
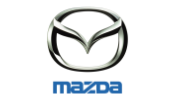
Intelligent assembly and adjustment line for four doors and two covers of white body
The full process intelligent flexible car door cover assembly and adjustment production line is independently developed and the first to achieve mass production in China. The production efficiency of the entire line reaches 60JPH (54 seconds), and the production capacity of the entire line reaches 8 car models for random mixed production. This assembly line uses a flexible NC positioning system to seamlessly connect the positioning and grabbing of the chassis and door covers of each vehicle type. Machine vision technology is used to achieve precise grabbing, positioning, measurement, and assembly. Ultra high speed transmission technology is used to create a record of 18 white body engineering transfers completed within 4 seconds!
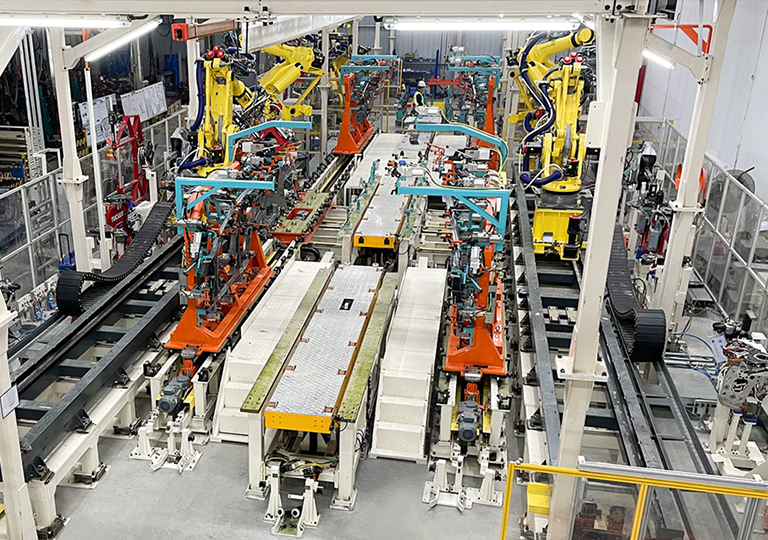
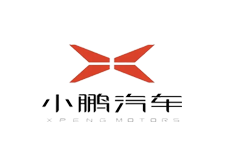
New energy vehicle steel aluminum hybrid trial production line
Realize the welding, riveting, fusion, and automatic handling of mixed vehicle bodies made of various different metal materials such as steel and aluminum; Improved flexibility, able to meet the needs of multi vehicle mixed line trial production; The highest utilization rate of equipment has greatly improved the space utilization rate of the factory building; Improved the automation level and production efficiency of the production line; Through trial production, the optimal parameter settings for spot welding gun, FDS gun, and SPR gun were determined to achieve mixed production of vehicle bodies with different materials.
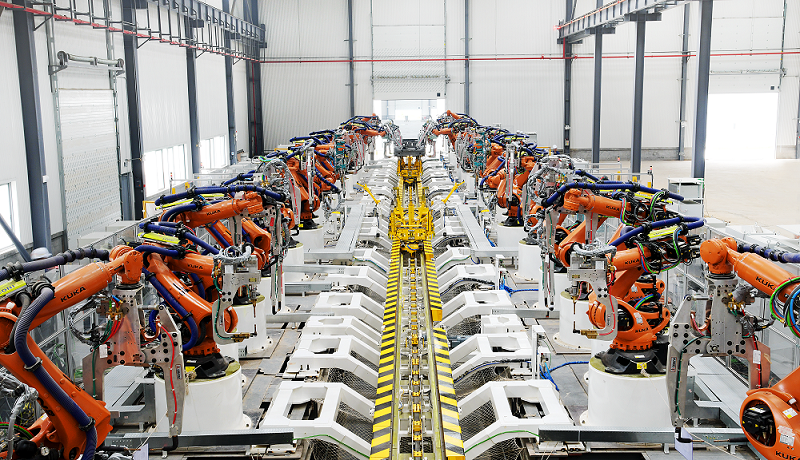
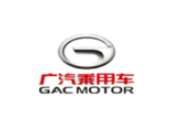
Flexible welding production line for white body of fuel powered vehicles
Using over 200 robots; Advanced technologies such as visual guidance, comprehensive servo positioning, flexible passive trolley, intelligent vehicle switching device, flexible rolling, and offline debugging have been comprehensively utilized; We have achieved highly unmanned production on the entire production line, which can meet the simultaneous production of 5 vehicle models and achieve intelligent seamless switching. The production cycle is 45 seconds per unit, reaching the leading domestic cycle level and vehicle switching speed.